Alcast Company for Dummies
Alcast Company for Dummies
Blog Article
Alcast Company - Truths
Table of ContentsAlcast Company Fundamentals ExplainedThe Main Principles Of Alcast Company The Ultimate Guide To Alcast CompanyAlcast Company for BeginnersThe Best Strategy To Use For Alcast CompanyWhat Does Alcast Company Mean?
Chemical Comparison of Cast Light weight aluminum Alloys Silicon advertises castability by minimizing the alloy's melting temperature and improving fluidity throughout spreading. Furthermore, silicon adds to the alloy's toughness and use resistance, making it useful in applications where toughness is essential, such as vehicle parts and engine components.It likewise improves the machinability of the alloy, making it less complicated to refine into ended up products. This way, iron adds to the total workability of aluminum alloys. Copper raises electrical conductivity, making it helpful in electric applications. It additionally improves corrosion resistance and contributes to the alloy's general toughness.
Manganese contributes to the strength of light weight aluminum alloys and improves workability. Magnesium is a light-weight aspect that gives stamina and impact resistance to aluminum alloys.
The Facts About Alcast Company Uncovered
It enables the production of light-weight elements with exceptional mechanical buildings. Zinc improves the castability of aluminum alloys and helps control the solidification procedure throughout casting. It improves the alloy's stamina and firmness. It is often located in applications where complex forms and great details are necessary, such as attractive spreadings and certain auto components.
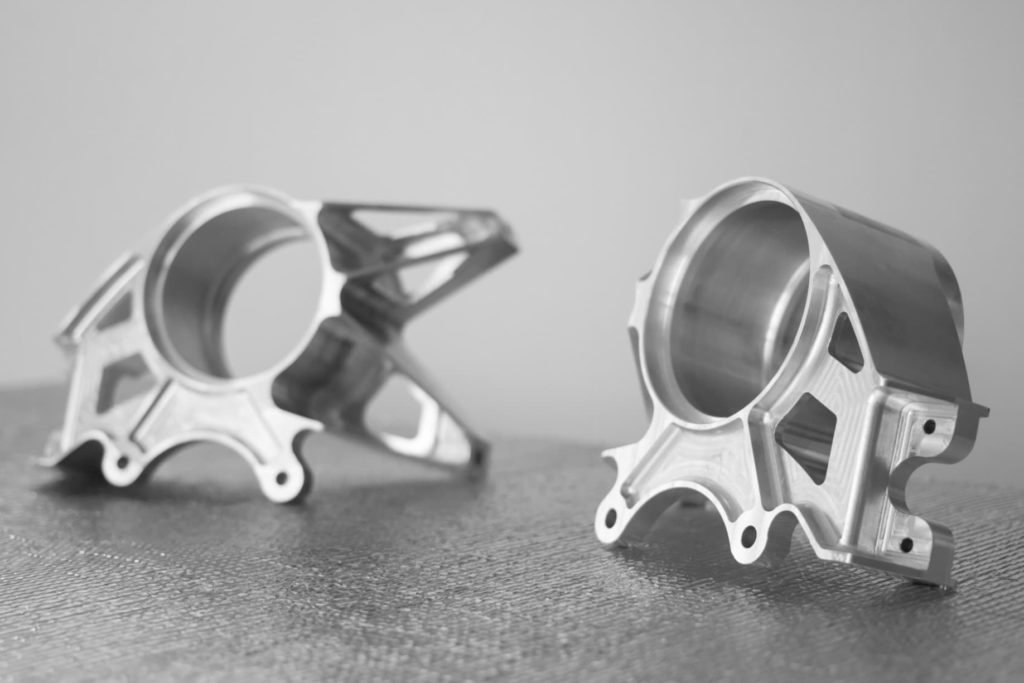
The key thermal conductivity, tensile toughness, yield strength, and prolongation vary. Select appropriate raw products according to the efficiency of the target item produced. Amongst the above alloys, A356 has the greatest thermal conductivity, and A380 and ADC12 have the most affordable. The tensile restriction is the opposite. A360 has the finest return toughness and the highest prolongation price.
The Facts About Alcast Company Uncovered
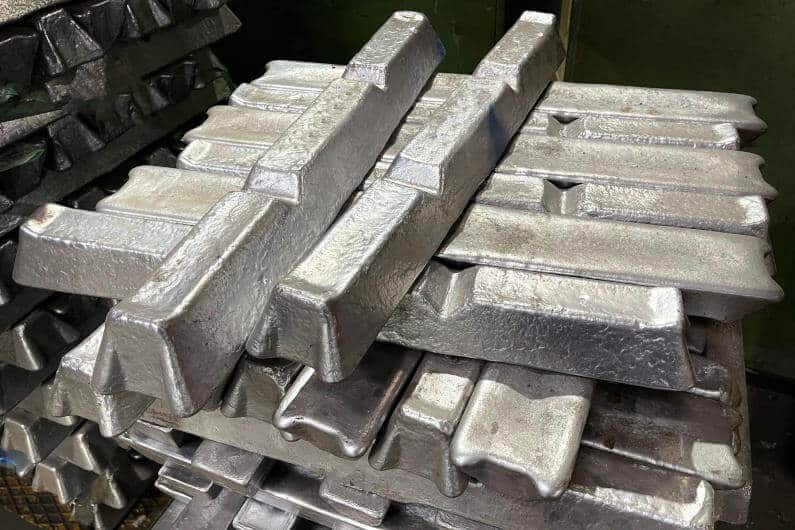
In accuracy casting, 6063 is well-suited for applications where elaborate geometries and high-quality surface finishes are vital. Examples include telecommunication rooms, where the alloy's exceptional formability permits for streamlined and cosmetically pleasing styles while keeping architectural integrity. Similarly, in the Illumination Solutions industry, precision-cast 6063 components create elegant and reliable illumination components that need intricate forms and great thermal performance.
It causes a finer surface finish and better rust resistance in A360. The A360 shows exceptional prolongation, making it suitable for complicated and thin-walled components. In accuracy spreading applications, A360 is well-suited for sectors such as Customer Electronic Devices, Telecommunication, and Power Devices. Its boosted fluidity enables for intricate, high-precision parts like mobile phone cases and communication device real estates.
The Best Strategy To Use For Alcast Company
Its distinct residential properties make A360 an important selection for precision casting in these markets, enhancing product resilience and quality. Light weight aluminum alloy 380, or A380, is a widely used casting alloy with several unique characteristics. It provides exceptional castability, making it a suitable choice for precision spreading. A380 shows excellent fluidity when molten, ensuring complex and recommended you read detailed molds are properly recreated.
In precision casting, light weight aluminum 413 radiates in the Customer Electronics and Power Equipment industries. This alloy's remarkable corrosion resistance makes it a superb choice for outside applications, making sure durable, resilient items in the stated sectors.
Alcast Company Fundamentals Explained
Once you have actually decided that the light weight aluminum die casting process is suitable for your task, an important next step is choosing on the most suitable alloy. The light weight aluminum alloy you choose will significantly impact both the spreading procedure and the residential or commercial properties of the last product. As a result of this, you need to make your decision thoroughly and take an enlightened approach.
Figuring out the most suitable light weight aluminum alloy for your application will suggest weighing a wide variety of characteristics. The very first classification addresses alloy features that influence the production process.
Alcast Company Things To Know Before You Buy
The alloy you pick for die spreading directly affects a number of elements of the spreading procedure, like exactly how very easy the alloy is to collaborate with and if it is vulnerable to casting problems. Hot fracturing, additionally referred to as solidification fracturing, is a typical die casting issue for aluminum alloys that can result in internal or surface-level splits or cracks.
Certain aluminum alloys are much more susceptible to warm splitting than others, and your choice should consider this. An additional usual defect found in the die casting of light weight aluminum is pass away soldering, which is when the cast adheres to the die wall surfaces and makes ejection hard. It can harm both the actors and the die, so you ought to seek alloys with high anti-soldering buildings.
Rust resistance, which is currently a remarkable feature of light weight aluminum, can vary substantially from alloy to alloy and is a crucial particular to take into consideration relying on the ecological problems your product will be revealed to (aluminum metal casting). Use resistance is another property frequently looked for in light weight aluminum items and can differentiate some alloys
Report this page